For Power Plants That Can’t Afford Downtime: OT Insights & Managed Services
When you’re responsible for the performance of a power generation plant, your focus is on keeping SCADA systems, PLCs, DCSs, RTUs, and HMIs running flawlessly. These critical systems demand constant precision, complete visibility, and absolutely no margin for error.
But even with a strong team, things slip through:
- Documentation gets outdated
- Vendors come and go without clear guardrails or oversight
- Backups go untested or fail silently
- Patches and upgrades fall behind
- Compliance becomes a manual grind
- Access control lacks clear ownership or enforcement
Individually, these issues might seem manageable. But they build up—and when they do, the risk often goes unnoticed until it hits: downtime, data loss, or non-compliance.
That’s why ProArch created Operational Technology Insights and Managed Services (OTIMS). OTIMS delivers structure, visibility, and proactive support across your entire OT environment—no matter the vendor or system. With OTIMS, you’re not just reacting to problems; you’re prepared for what’s next.
This post breaks down:
- Why traditional OT environments tend to drift into disorder
- The real risks that often go unnoticed until it’s too late
- How OTIMS transforms the approach from reactive to resilient
What OTIMS Actually Is (And What It’s Not)
OTIMS is a managed service that gives you full control and visibility over your OT environment without the overhead. Think, IT Managed Services, but from a Managed Services Provider (MSP) who deeply understands the role of IT in OT environments.
It works across everything: SCADA, DCS, PLCs, HMIs, RTUs, historian platforms, BoP systems, and the vendors that touch them. Instead of juggling disconnected tools and guessing who changed what, you get one clear layer of visibility, alerts when something goes wrong, and control over access, updates, and network health.
No more surprises. No more scrambling during audits. Just a clean, connected way to run your OT systems reliably and securely.
Why Traditional OT Environments Drift into Disorder
OT environments weren’t designed for frequent change; they were built to run continuously. Systems like SCADA, PLCs, and DCSs are expected to stay online with minimal updates. Why? Because uptime is critical. In OT, downtime doesn’t just delay work — it halts production, can compromise safety, and risks regulatory violations. In OT, availability matters most. It’s more important than keeping data confidential or perfectly accurate, which is just the opposite of how IT usually works.
But that focus on availability comes at a cost. Ownership is often fragmented: IT manages the network, engineering owns the control systems, and vendors work independently. There’s rarely unified visibility, which means changes go undocumented, backups go untested, and access is poorly tracked.
As more vendors, protocols, and compliance requirements pile on, even well-maintained environments become hard to manage. Teams end up relying on in-house knowledge and manual workarounds just to stay operational. Over time, the cracks deepen and drift becomes inevitable.
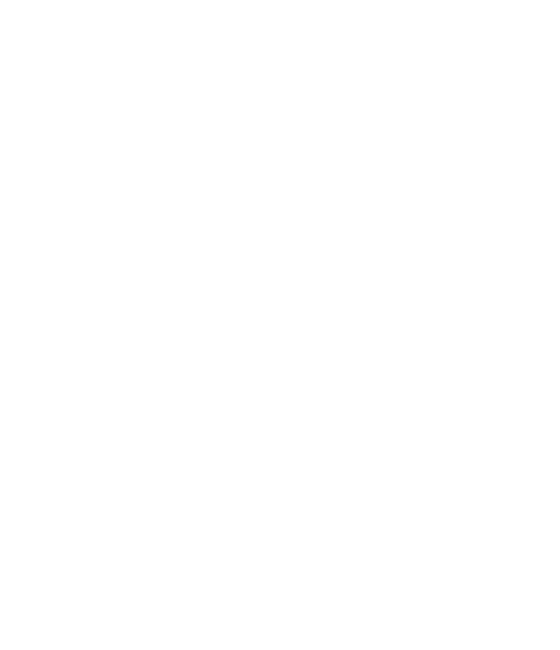
Struggling with OT visibility and compliance in your plant?
Get a technical assessment focused on your SCADA, PLC, and DCS environment.
What Your Plant is Up Against — And How OTIMS Helps
1. Limited Visibility
The issue: In most industrial environments, OT teams lack real-time visibility into their systems. They depend on outdated inventories that only list device types, firmware versions, and IP addresses. That’s not enough. Critical systems like SCADA, DCS, PLCs, HMIs, RTUs run in silos. There’s no unified view, no alerts when things break, and no way to track changes.
How OTIMS helps: OTIMS breaks the limits of static asset lists. It delivers a centralized, live map of your OT environment, tracking system health, data flows, configuration changes, and who accessed what, all in real time, with security and accountability. No more guessing. We can see what’s happening now and stop issues before they spiral.
2. Unmonitored Access and Isolated Vendor Systems
The issue: Multiple vendor-installed systems often run in isolation, each with its own remote access methods and little to no oversight or integration. Access control is spotty at best, and vendors maintain remote access with zero visibility into their actions or whether it’s even necessary.
How OTIMS helps: ProArch ensures that all third-party vendor access is secure and authenticated through OTIMS. No open doors, no unmanaged connections — just clear, controlled access every time.
For our own internal support teams, we take it a step further with session recording, multi-factor authentication (MFA), and strict access controls to ensure every action is accountable.
This gives the client’s security and operations teams the visibility, control, and peace of mind they need to manage risk with confidence and stay aligned with compliance requirements.
3. Limited Traceability
The issue: In OT environments, when something goes wrong, there’s often no record of what changed, who changed it, or when it happened. Without an audit trail, teams can’t respond quickly, leading to longer downtime and increased risk to critical operations.
How OTIMS helps: OTIMS has your back, quietly tracking every system change like PLC updates, DCS tweaks, firmware swaps and logging them neatly for quick, stress-free root cause analysis.
4. Unreliable Patching & Backups
The issue: Let’s be real, backups and security patches are often skipped, forgotten, or untested. You won’t know if you can recover until it’s too late.
How OTIMS helps: OTIMS Automates patching and importantly does that with tested backup restores so you’re protected and covered if something fails.
5. Chaos of Manual Compliance
The issue: Compliance frameworks like NERC-CIP, FDA 21 CFR Part 11, and GMP demand evidence, standardized controls and sometimes, unexpected questions answered. Yet most plants still rely on manual, disconnected processes, making audits reactive and error-prone, and turning a Reliability Entity’s inquiry into a scramble for answers.
How OTIMS helps: OTIMS enforces standardized security and operational controls across all generation assets. It continuously logs system activity creating an asset database, alerts on configuration changes, and user access to maintain alignment with regulatory requirements ensuring audit readiness without last-minute efforts.
6. Too much reliance on Key Staff
The issue: System knowledge, network configurations, and access credentials are often undocumented and limited to a few staff. Their absence creates operational and recovery delays.
How OTIMS helps: OTIMS neatly centralizes documentation, access control, and system workflows. It’s custom-built to bridge the gaps when documentation is spotty or missing altogether. Plus, it comes with expert support to bring the technical know-how needed to keep operations running smoothly without a hitch.
7. Hard to Identify Root Cause
The issue: OT systems include many components like PLCs, HMIs, SCADA, sensors, and network switches. These systems often run in silos with limited logs, no central monitoring, and little real-time visibility. When something fails, there is no clear record of what went wrong, when it happened, or where it started. Teams have to troubleshoot manually, moving between different systems and guessing the cause. This wastes time and increases the risk of extended downtime.
How OTIMS helps: OTIMS gives you clear system alerts and diagnostics across your entire site. Your team can quickly find underperforming assets and identify the real problem. If something goes down, backups are ready, tested, and easy to restore.
How OTIMS Helped a Power Plant Strengthen Security and Regain Control After Ownership Change
A 309MW gas-fired power plant faced a critical transition after a change in ownership. Previously supported under a corporate IT umbrella, the new owner had just six weeks to take full control—migrating systems, securing infrastructure, and eliminating legacy vendor access.
Through ProArch’s OTIMS program, our team led the transition end to end. We rebuilt the network infrastructure, migrated user systems, reconfigured firewalls and switches, and conducted a full OT Threat Assessment. Several vulnerabilities were uncovered, including active backdoors left by prior vendors. SecureLink was deployed to manage and audit third-party remote access.
The result: A complete IT/OT transition was delivered on schedule and without disruption—demonstrating how OTIMS accelerates secure operational handoffs while eliminating inherited risks that often go unnoticed. Read the whole story
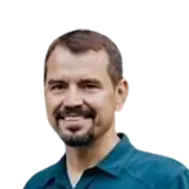
Talk to our OT expert about improving visibility, control, and resilience across your OT stack.
Luke Bixby
VP, Industry Solutions
Have the visibility to operate with confidence, reliability, and resilience
OTIMS isn’t just another monitoring layer, it’s ProArch’s full-stack approach to OT/IT security and operational maturity. Built for environments that can’t afford guesswork, downtime, or disconnected systems.
With OTIMS, your SCADA, DCS, PLCs, RTUs, HMIs, and vendor tools are unified under one secure, documented, and supported framework. You know what’s connected, who has access, what changed, and what’s at risk before it becomes a problem.
We don’t just manage one part of your stack. We connect the dots. ProArch delivers a holistic view of your entire OT/IT environment, backed by 24/7 monitoring, compliance-ready documentation, and deep operational expertise.

Assistant Manager Content Parijat helps shape ProArch’s brand voice, turning complex tech concepts into clear, engaging content. Whether it’s blogs, email campaigns, or social media, she focuses on making ProArch’s messaging accessible and impactful. With experience in Oracle, Cloud, and Salesforce, she blends creativity with technical know-how to connect with the right audience. Beyond writing, she ensures consistency in how ProArch tells its story—helping the brand stay strong, authentic, and aligned with its vision.